Categories
Contact
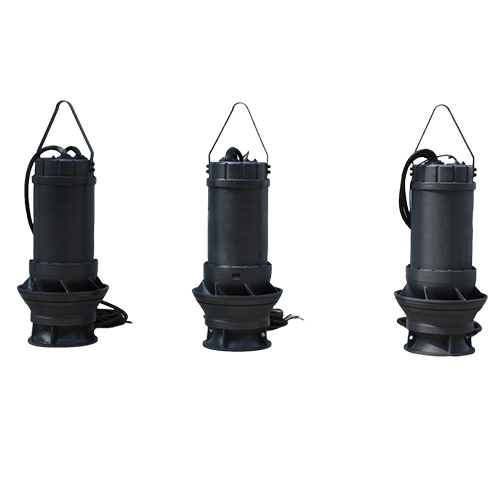
Vertical Axial Flow Pump
Vertical axial flow pumps are specialized hydraulic machines designed to move large volumes of fluid efficiently in a vertical direction. These pumps play a crucial role in various industries, including water treatment, irrigation, flood control, and power generation. Understanding their construction, operation, advantages, and leading manufacturers can help engineers and decision-makers select the most appropriate pumping solution for their specific needs.
The construction of vertical axial flow pumps is characterized by a unique design that allows for efficient fluid movement in an axial direction. At the heart of these pumps is a vertical shaft with impeller blades attached. The shaft is typically supported by bearings at both ends to ensure smooth rotation and minimize vibration. The impeller, which is the key component responsible for fluid movement, is mounted on the lower end of the shaft.
The impeller blades are carefully designed and engineered to optimize fluid flow. They are typically curved or twisted to create the most effective fluid acceleration. The number of blades can vary depending on the specific pump design and application requirements, but most vertical axial flow pumps have between three and six blades.
Surrounding the impeller is a stationary casing, often referred to as the pump bowl. This casing is designed to guide the fluid flow and house the impeller assembly. The pump bowl is usually made of durable materials such as cast iron, stainless steel, or bronze to withstand the pressures and potential corrosive effects of the pumped fluid.
Above the impeller and pump bowl is the discharge column, which directs the pumped fluid upwards. The length of this column can vary depending on the installation depth and pumping requirements. At the top of the pump assembly is the discharge head, where the fluid exits the pump and is directed into the connected piping system.
The motor that drives the vertical axial flow pump is typically mounted above the discharge head on a substantial baseplate. This arrangement keeps the motor away from potential flooding and allows for easy access for maintenance. The motor is connected to the pump shaft through a coupling system, which may include a flexible coupling to accommodate minor misalignments and reduce vibration transmission.
Model | Vane Angle | Capacity (m³/h) | Head (m) | Power (Kw) | Speed (r/min) | Effciency (%) | Outer diameter of impeller (mm) |
350QZ-50 | 0° | 1173 | 10 | 55 | 1450 | 81 | 300 |
500QZ-75 | 0° | 3045 | 7 | 90 | 980 | 72 | 450 |
600QZ-100 | 0° | 3736 | 3.6 | 75 | 740 | 82 | 550 |
700QZ-100 | 0° | 4850 | 4.3 | 110 | 740 | 73 | 600 |
800QZ-50 | 0° | 6066 | 9 | 220 | 590 | 84 | 700 |
800QZ-135 | 0° | 6617 | 2.9 | 110 | 590 | 83 | 700 |
900QZ-50 | 0° | 7461 | 10 | 315 | 590 | 84 | 750 |
1000QZ-35 | 0° | 11571 | 15 | 630 | 490 | 85 | 870 |
1200QZ-50 | 0° | 12593 | 11 | 560 | 490 | 85 | 950 |
350QH-72 | 0° | 837 | 2.87 | 15 | 980 | 80 | 300 |
500QH-40 | 0° | 3200 | 16.55 | 200 | 980 | 83 | 450 |
600QH-35 | 0° | 4415 | 14.29 | 250 | 740 | 84 | 550 |
700QH-72 | 0° | 5056 | 6.54 | 160 | 740 | 84 | 600 |
800QH-72 | 0° | 6401 | 5.66 | 185 | 590 | 83 | 700 |
900QH-35 | 0° | 10791 | 14.96 | 630 | 490 | 85 | 850 |
1000QH-72 | -2° | 8871.5 | 6.09 | 250 | 490 | 85 | 870 |
1200QH-72 | +4° | 15607 | 8.45 | 560 | 490 | 86 | 950 |
1300QH-72 | +6° | 22198 | 7.79 | 710 | 370 | 85.8 | 1150 |
Operation
The operation of vertical axial flow pumps is based on the principle of axial fluid acceleration. When the pump is activated, the motor turns the vertical shaft, causing the impeller to rotate within the pump bowl. As the impeller spins, its blades are designed to accelerate the fluid axially – that is, parallel to the pump shaft.
As the fluid flows through the impeller, it gains both velocity and pressure. The curved design of the impeller blades creates a low-pressure area on one side and a high-pressure area on the other, effectively "lifting" the fluid and propelling it upwards. This action creates a continuous flow of fluid through the pump.
After passing through the impeller, the high-velocity fluid enters the diffuser. The diffuser is a critical component located downstream of the impeller, typically integrated into the pump bowl or discharge column. Its primary function is to convert the kinetic energy of the fast-moving fluid into pressure energy.
The diffuser accomplishes this conversion through a carefully designed series of expanding passages. As the fluid moves through these passages, its velocity gradually decreases while its pressure increases. This process is based on Bernoulli's principle, which states that in fluid dynamics, an increase in the speed of a fluid occurs simultaneously with a decrease in pressure or a decrease in the fluid's potential energy.
The now high-pressure, lower-velocity fluid continues its journey up the discharge column and out through the discharge head. From there, it enters the connected piping system for distribution to its intended destination, whether that's a water treatment plant, irrigation system, or other application.
It's worth noting that the efficiency of this operation depends on several factors, including the design of the impeller and diffuser, the rotational speed of the pump, and the characteristics of the fluid being pumped. Engineers must carefully consider these factors when selecting and implementing vertical axial flow pumps to ensure optimal performance.
Advantages of using a vertical axial flow pump
Vertical axial flow pumps offer several significant advantages that make them the preferred choice for many large-scale pumping applications:
High Flow Rate: One of the primary advantages is their ability to handle very high flow rates. These pumps are designed to move large volumes of fluid efficiently, making them ideal for applications such as flood control, irrigation systems, and cooling water circulation in power plants.
Low Head Applications: they excel in low to medium head applications. While they may not generate as much pressure as some other pump types, they can move enormous quantities of fluid against relatively low head pressures, which is perfect for many water management scenarios.
Energy Efficiency: Due to their design, they can be highly energy-efficient, especially when operating at their best efficiency point. This can lead to significant energy savings over time, particularly in large-scale operations where pumps run continuously.
Space Efficiency: The vertical configuration of these pumps makes them very space-efficient. They have a relatively small footprint compared to their pumping capacity, which can be a crucial advantage in installations where space is limited.
Submerged Operation: Many vertical axial flow pumps are designed to operate while partially or fully submerged. This makes them excellent choices for applications like flood control or pumping from deep wells or reservoirs.
Minimal Cavitation Risk: The design of vertical axial flow pumps, particularly the placement of the impeller near or below the water surface, reduces the risk of cavitation. This can lead to longer pump life and more reliable operation.
Ease of Maintenance: In many designs, the motor and other critical components are located above the water level, making them easier to access for maintenance and repairs without the need to remove the entire pump assembly.
Versatility: Vertical axial flow pumps can handle a wide range of fluids, including water, wastewater, and various industrial liquids. This versatility makes them valuable across multiple industries.
Durability: When properly designed and maintained, vertical axial flow pumps can be extremely durable and long-lasting, even in challenging operating conditions.
Scalability: These pumps can be designed and manufactured in a wide range of sizes, from relatively small units for industrial applications to massive pumps for flood control or hydroelectric projects.
Vertical axial flow pump manufacturers
Tianjin Kairun has developed a comprehensive quality assurance system that covers every aspect of their pump production, from initial development and design through manufacturing and testing, all the way to after-sales service. This holistic approach to quality control helps ensure that their vertical axial flow pumps meet the highest standards of performance and reliability.
The company's commitment to quality begins at the development stage, where engineers work to create innovative designs that meet specific customer needs while adhering to industry standards. Their design process incorporates the latest in fluid dynamics modeling and materials science to optimize pump performance and efficiency.
During the manufacturing phase, Tianjin Kairun employs advanced production techniques and rigorous quality control measures. Each component is carefully inspected to ensure it meets precise specifications before assembly. The use of high-quality materials and precision machining helps to ensure the longevity and reliability of their pumps.
Testing is a critical part of Tianjin Kairun's quality assurance process. Each pump undergoes thorough performance testing to verify that it meets or exceeds the specified performance criteria. This may include tests for flow rate, pressure, efficiency, and durability under various operating conditions.
Perhaps one of the most important aspects of Tianjin Kairun's service is their commitment to after-sales support. They understand that the purchase of a vertical axial flow pump is a significant investment, and they strive to support their customers throughout the life of the pump. This includes providing technical assistance, maintenance support, and rapid response to any issues that may arise.
For those in the market for vertical axial flow pumps, Tianjin Kairun welcomes inquiries and is ready to assist with selecting the right pump for specific applications. They can be contacted at catherine@kairunpump.com for more information about their products and services.
References:
1. Karassik, I. J., Messina, J. P., Cooper, P., & Heald, C. C. (2008). Pump Handbook (4th ed.). McGraw-Hill Education.
2. Gülich, J. F. (2020). Centrifugal Pumps (3rd ed.). Springer.
3. Tuzson, J. (2000). Centrifugal Pump Design. John Wiley & Sons.
4. Lobanoff, V. S., & Ross, R. R. (2013). Centrifugal Pumps: Design and Application (2nd ed.). Elsevier.
5. Nelik, L. (1999). Centrifugal and Rotary Pumps: Fundamentals with Applications. CRC Press.