Categories
Contact
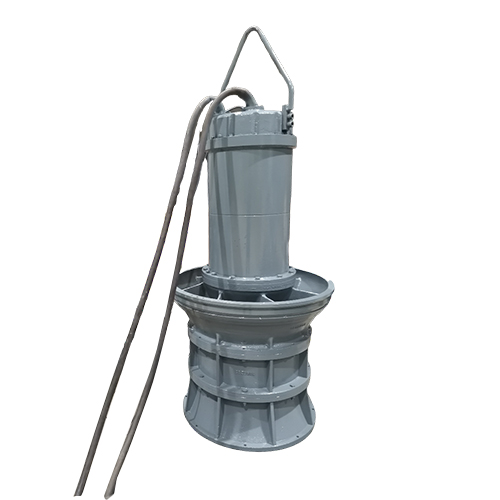
Axial Flow Submersible Water Pump
Axial flow submersible water pumps are essential components in various industrial applications, particularly where high flow rates and low to moderate heads are required.
Axial flow submersible water pumps are widely used in irrigation systems, flood control, cooling water circulation in power plants, and wastewater treatment facilities. Understanding the working principle of axial flow submersible water pumps is crucial for engineers, technicians, and operators involved in fluid handling systems.
Parameter information sheet
Model | Vane Angel | Capacity (m3/h) | Head (m) | Power (KW) | Speed (r/min) | Effciency (%) | Outer diameter of impeller (mm) |
350QZ-50G | 0° | 1173.6 | 10.1 | 55 | 1450 | 81.8 | 300 |
350QZ-100D | 0° | 802.9 | 1.92 | 11 | 1450 | 79.5 | 300 |
500QZ-50G | 0° | 2677 | 10.38 | 110 | 980 | 83.3 | 450 |
600QZ-50 | 0° | 3690.7 | 8.84 | 132 | 740 | 83.7 | 550 |
700QZ-75 | 0° | 5451.5 | 7.33 | 160 | 740 | 83.9 | 600 |
800QZ-100 | 0° | 6140.9 | 3.79 | 110 | 590 | 83.8 | 700 |
900QZ-160D | 0° | 9961.5 | 2.29 | 110 | 490 | 82.4 | 850 |
1000QZ-35 | 0° | 11571.5 | 15.67 | 630 | 490 | 85.8 | 870 |
1200QZ-135 | 0° | 13737.2 | 3.72 | 250 | 490 | 84.4 | 950 |
1300QZ-50 | 0° | 16868.8 | 9.66 | 630 | 370 | 86 | 1150 |
1400QZ-100 | 0° | 19401.3 | 4.39 | 400 | 370 | 85.7 | 1200 |
1600QZ-75 | 0° | 32616.3 | 7.09 | 900 | 295 | 86.5 | 1480 |
Lift generated by the impeller
The primary working principle of an axial flow submersible water pump is based on the concept of lift generation, similar to how an airplane wing produces lift in air. As the impeller rotates within the fluid, it creates a pressure difference between the upper and lower surfaces of its blades. This pressure differential results in a lifting force that propels the fluid axially through the pump.
The impeller blades are designed with a specific shape and angle of attack to optimize this lift generation. As the impeller rotates, the fluid is accelerated and guided along the axis of the pump. The rotational motion of the impeller imparts both axial and tangential velocity components to the fluid. The axial component is responsible for the pumping action, while the tangential component is typically converted into additional pressure energy by the pump's stationary components
The efficiency of this lift-based pumping mechanism depends on various factors, including the impeller design, rotational speed, and fluid properties. By carefully controlling these parameters, axial flow submersible water pumps can achieve high flow rates with relatively low energy input, making them ideal for applications requiring the movement of large volumes of fluid.
Function of the impeller
The impeller is the heart of an axial flow submersible water pump and plays a crucial role in the energy conversion process. As the prime mover (typically an electric motor or engine) rotates the impeller, it transfers mechanical energy to the fluid. This energy is converted into two forms: pressure energy and kinetic energy.
The impeller blades are designed with an airfoil-like cross-section, similar to airplane wings. As the fluid flows over these airfoil-shaped blades, it experiences a pressure difference between the upper and lower surfaces. This pressure differential creates lift, which propels the fluid axially through the pump.
The kinetic energy imparted to the fluid is manifested as increased velocity in both the axial and tangential directions. The axial velocity component contributes directly to the pump's flow rate, while the tangential component is often considered a loss that needs to be minimized or recovered.
The efficiency of the impeller in converting mechanical energy to fluid energy depends on several factors, including:
1. Blade geometry (angle, curvature, and thickness)
2. Number of blades
3. Impeller diameter
4. Rotational speed
5. Fluid properties (viscosity, density)
Engineers optimize these parameters to achieve the desired pump performance while minimizing energy losses and cavitation risks.
The function of the guide vane
After the fluid passes through the impeller, it possesses both axial and rotational velocity components. The guide vanes, also known as stator blades or diffuser vanes, play a critical role in optimizing the axial flow submersible water pump's overall efficiency by addressing this rotational flow.
The primary functions of the guide vanes are:
1. Flow straightening: The guide vanes redirect the spiraling fluid exiting the impeller into a more axial direction. This flow straightening reduces energy losses associated with swirling flow and improves the axial flow submersible water pump's hydraulic efficiency.
2. Energy conversion: As the fluid passes through the guide vanes, a portion of its kinetic energy (primarily the rotational component) is converted into pressure energy. This conversion process is achieved through careful design of the guide vane geometry, which effectively acts as a diffuser.
3. Pressure recovery: By slowing down the fluid and expanding the flow area, the guide vanes help recover pressure that would otherwise be lost. This pressure recovery contributes to the overall head generated by the pump.
4. Flow stability: Well-designed guide vanes can help stabilize the flow within the pump, reducing turbulence and improving overall pump performance.
The effectiveness of the guide vanes in performing these functions depends on their design, including factors such as the number of vanes, their shape, angle, and spacing. Proper alignment between the impeller and guide vanes is also crucial for optimal performance.
Performance Characteristics
To ensure safe and efficient operation of axial flow submersible water pumps, operators should:
1. Avoid prolonged operation in the unstable low flow region
2. Always start the pump with an open discharge valve
3. Monitor pump performance and system conditions to maintain operation near the design point
4. Implement proper control strategies, such as variable speed drives, to accommodate varying system demands while maintaining efficient operation