Categories
Contact
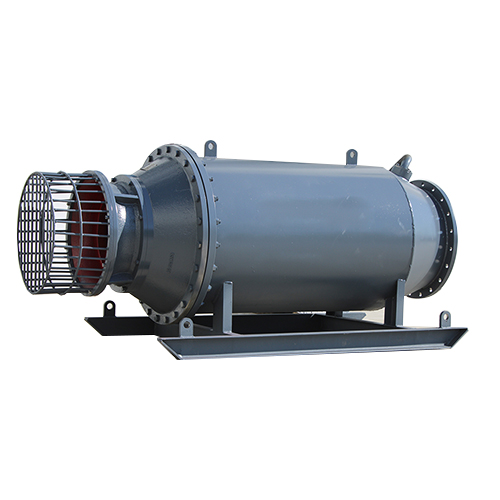
Axial Flow Pumps
Differences between centrifugal and axial flow pumps technologies in terms of theoretical basis, design considerations, areas of application, etc.
Centrifugal and axial flow pumps are two fundamental types of dynamic pumps that play crucial roles in various industries and applications. These pumps are essential for moving fluids in diverse settings, from water supply systems and irrigation to industrial processes and power generation. Understanding the theory, design principles, and applications of these pumps is vital for engineers, technicians, and decision-makers involved in fluid handling systems.
Theoretical Basis
The working principles of axial flow pumps and centrifugal pumps differ significantly, which leads to their distinct performance characteristics and applications. Axial flow pumps, as the name suggests, propel fluid along the pump axis through the impeller. The impeller in an axial flow pump resembles a propeller, with blades designed to impart kinetic energy to the fluid in a direction parallel to the shaft. This design allows for high flow rates but typically produces lower pressure increases.
On the other hand, centrifugal pumps utilize centrifugal force to expel fluid radially from the impeller. As the impeller rotates, it imparts both velocity and pressure to the fluid. The fluid enters the pump near the center of the impeller (the eye) and is then flung outward by centrifugal force. This radial movement creates a low-pressure area at the impeller eye, drawing more fluid into the pump. The volute or diffuser section of the pump then converts the fluid's velocity into pressure energy.
The design of centrifugal pumps involves a deep understanding of fluid dynamics and the physical principles governing pump operation. This includes considerations of flow patterns within the impeller and casing, pressure distribution, and energy transfer mechanisms. Engineers must also account for factors such as cavitation, hydraulic losses, and the pump's behavior under various operating conditions.
Acceptance testing and performance prediction are crucial aspects of pump design and selection. This involves developing and utilizing planning data that accurately represent the pump's performance for specific applications. Such data typically includes pump curves showing the relationship between flow rate, head, efficiency, and power consumption across the pump's operating range.
Model | Vane Angle | Capacity (m³/h) | Head (m) | Power (Kw) | Speed (r/min) | Effciency (%) | Outer diameter of impeller (mm) |
350QZ-50 | 0° | 1173 | 10 | 55 | 1450 | 81 | 300 |
500QZ-75 | 0° | 3045 | 7 | 90 | 980 | 72 | 450 |
600QZ-100 | 0° | 3736 | 3.6 | 75 | 740 | 82 | 550 |
700QZ-100 | 0° | 4850 | 4.3 | 110 | 740 | 73 | 600 |
800QZ-50 | 0° | 6066 | 9 | 220 | 590 | 84 | 700 |
800QZ-135 | 0° | 6617 | 2.9 | 110 | 590 | 83 | 700 |
900QZ-50 | 0° | 7461 | 10 | 315 | 590 | 84 | 750 |
1000QZ-35 | 0° | 11571 | 15 | 630 | 490 | 85 | 870 |
1200QZ-50 | 0° | 12593 | 11 | 560 | 490 | 85 | 950 |
350QH-72 | 0° | 837 | 2.87 | 15 | 980 | 80 | 300 |
500QH-40 | 0° | 3200 | 16.55 | 200 | 980 | 83 | 450 |
600QH-35 | 0° | 4415 | 14.29 | 250 | 740 | 84 | 550 |
700QH-72 | 0° | 5056 | 6.54 | 160 | 740 | 84 | 600 |
800QH-72 | 0° | 6401 | 5.66 | 185 | 590 | 83 | 700 |
900QH-35 | 0° | 10791 | 14.96 | 630 | 490 | 85 | 850 |
1000QH-72 | -2° | 8871.5 | 6.09 | 250 | 490 | 85 | 870 |
1200QH-72 | +4° | 15607 | 8.45 | 560 | 490 | 86 | 950 |
1300QH-72 | +6° | 22198 | 7.79 | 710 | 370 | 85.8 | 1150 |
Design Considerations
When designing axial flow and centrifugal pumps, engineers must balance numerous factors to achieve optimal performance. Pump efficiency is a primary concern, as it directly impacts energy consumption and operating costs. The required flow rate and head (pressure increase) are fundamental parameters that dictate the overall pump design, including impeller geometry and casing configuration.
Impeller design is critical for both pump types. In axial flow pumps, the impeller blades are shaped to efficiently transfer energy to the fluid while minimizing turbulence and hydraulic losses. Centrifugal pump impellers may be open, semi-open, or closed, with the choice depending on the specific application and fluid properties.
Pump speed is another crucial design parameter. Higher speeds generally allow for smaller, more compact pumps but may introduce challenges related to cavitation, wear, and noise. The specific speed of a pump, a dimensionless parameter that relates flow rate, head, and rotational speed, is often used to classify pumps and guide design decisions.
Fluid properties, particularly viscosity and specific gravity, significantly influence pump performance and must be carefully considered in the design process. Viscous fluids, for example, may require special impeller designs or larger clearances to maintain efficiency.
Model laws, such as affinity laws, play a vital role in pump design and scaling. These laws describe how pump performance changes with variations in impeller diameter or rotational speed, allowing engineers to predict performance across a range of operating conditions.
The stability of the pump within the overall system is another critical design consideration. This includes analyzing potential issues such as surging, cavitation, and hydraulic imbalance, which can affect pump reliability and efficiency.
Application Areas
Axial flow pumps excel in applications requiring high flow rates with relatively low pressure increases. Their ability to move large volumes of fluid efficiently makes them ideal for irrigation systems, where water needs to be distributed over large areas. In flood control applications, axial flow pumps are used to rapidly move water from flood-prone areas to storage basins or discharge points. Hydropower generation also utilizes axial flow pumps, often in reversible pump-turbine configurations, to manage water flow in pumped storage systems.
Centrifugal pumps, with their ability to generate higher pressures, find widespread use across numerous industries. In water supply systems, centrifugal pumps are used to move water from treatment plants to distribution networks, often overcoming significant elevation differences. Industrial processes rely heavily on centrifugal pumps for tasks such as chemical transfer, cooling system circulation, and slurry handling. HVAC systems employ centrifugal pumps to circulate chilled or hot water for climate control in large buildings. The oil and gas industry uses specialized centrifugal pumps for tasks ranging from pipeline transport to offshore platform operations.
Latest Developments
Recent advancements in pump design and technology have focused on improving efficiency, reliability, and versatility across a wide range of applications. Computational Fluid Dynamics (CFD) has become an invaluable tool in pump design, allowing engineers to optimize flow paths and reduce hydraulic losses with unprecedented precision.
Materials science has contributed to the development of pump components that can withstand increasingly challenging operating conditions. Advanced alloys and composite materials offer improved resistance to corrosion, erosion, and cavitation damage.
Innovations in sealing technology, such as magnetic drive pumps and advanced mechanical seals, have enhanced pump reliability and reduced the risk of leakage in critical applications.
The integration of smart technologies and IoT (Internet of Things) capabilities has revolutionized pump monitoring and maintenance. Advanced sensors and data analytics allow for real-time performance monitoring, predictive maintenance, and optimized operation based on system demands.
Improved testing and reliability procedures have led to more accurate performance predictions and longer pump lifespans. This includes advanced techniques for analyzing rotor vibration behavior and optimizing pump performance across various types of circuits.
Efforts to address cavitation and erosion have resulted in new impeller designs and materials that can better withstand these destructive phenomena. This has expanded the operating range of pumps and improved their longevity in challenging applications.
Energy efficiency remains a key focus area, with ongoing research into high-efficiency motor technologies, advanced control systems, and optimized hydraulic designs. Variable frequency drives (VFDs) have become increasingly common, allowing pumps to operate at their best efficiency point across a range of flow conditions.
Axial Flow Pump Manufacturers
In the competitive landscape of pump manufacturing, companies that prioritize innovation and customer satisfaction stand out. Tianjin Kairun is one such manufacturer that has built its reputation on the principles of "scientific and technological innovation, customer first, and the pursuit of excellence." Their commitment to continuous development ensures that their axial flow pumps incorporate the latest advancements in pump technology.
For those in the market for axial flow pumps, Tianjin Kairun welcomes inquiries at :catherine@kairunpump.com. This direct line of communication allows potential customers to discuss their specific requirements and explore how Tianjin Kairun's products might fit their applications.
References:
1. Gülich, J.F. Centrifugal Pumps. Springer Berlin Heidelberg.
2. Karassik, I.J., Messina, J.P., Cooper, P., & Heald, C.C. Pump Handbook. McGraw-Hill Education.
3. Tuzson, J. Centrifugal Pump Design. John Wiley & Sons.